Driven by electrification and the goal to reduce carbon emission, the integration of parts has gradually become the trend for the lightweight of car body. Supported by ArcelorMittal's global R&D capabilities, GONVVAMA has been at the forefront in offering lightweight solutions. In 2022 GONVVAMA officially brought its proven multi-part integration solution to the Chinese market, which uses pressed hardened steel (PHS), laser-welding technology and patches (if required) to create integrated parts. Hot-formed laser-welding double door rings, hot-formed laser-welding H-frame is a typical example of multi-part integration solutions. As a high-end electric auto brand of Dongfeng Group, Voyah has been committed to providing high-end and intelligent electric experience with zero anxiety. In order to achieve zero anxiety for the safety carbody, In 2021, voyah invited GONVVAMA, VAMA and ArcelorMittal China EVI eam to participate in the product design of the integrated door ring. The body-in-white of Voyah Dreamer, which adopts 2000Mpa integrated door ring, won the special honor award of China Body Conference in 2021. However, Voyah automobile never stops on the road of pursuing excellence. In order to create a safer, lighter and more environmental-friendly car body, in 2022, voyah again invited GONVVAMA, VAMA and ArcelorMittal China EVI team to participate in the joint pre-research of hot stamping laser-welded H-frame. Compared with the traditional body chassis manufacturing process, H-frame has the following advantages: • Greatly simplified vehicle production process • Different power systems can share a common, modular solution. • Improve vehicle crash resistance. • Significantly reduce carbon emissions and contribute to carbon neutrality. • Achieve cost savings of more than 10%. Take the rear H-frame of ArcelorMittal's S-In-Motion SUV as an example,H-frame converts 11 parts into a single laser-welded part, a solution that can be applied to almost any powertrain with the addition of a patch to strengthen local areas. With the H-frame, 136 spot welds can be eliminated per vehicle, and the floor area of the body shop in the OEMs can be reduced by half.The weight of each vehicle is also reduced by 1.4kg, which means less steel and less carbon dioxide emissions over the lifecycle of the vehicle.The combination of laser tailor-welding technology and hot stamping steel such as Usibor and Ductibor improves safety performance and ensures that the H-beam concept passes all crash test scenarios.
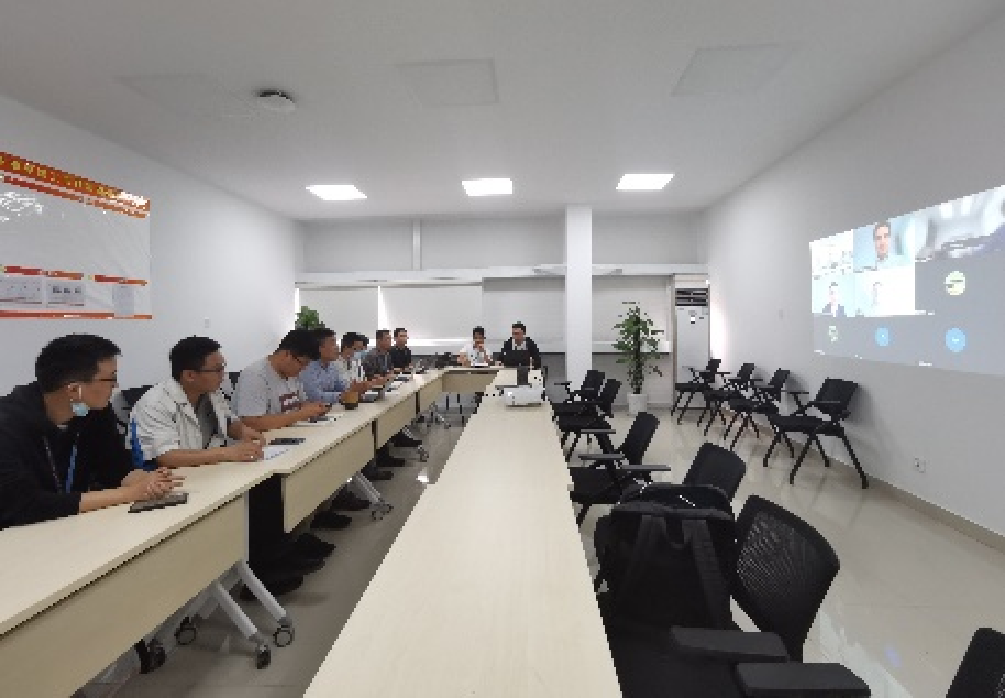
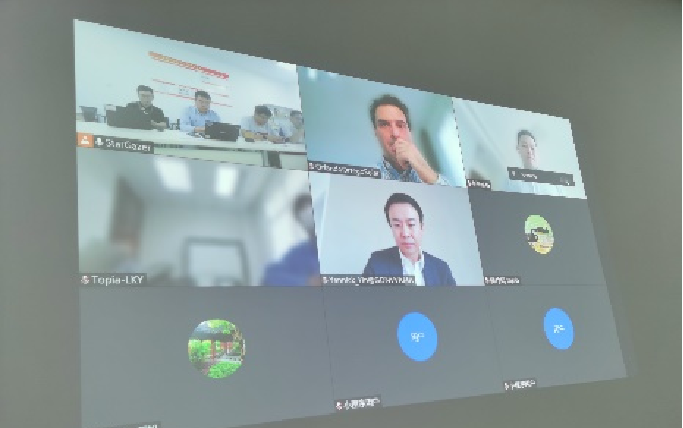