Laser Welded Blanks
● Laser welded blanks are two or more steel sheets welded together by a laser.
● These sheets can have:
- Different thicknesses
- Different alloys
- Different coatings
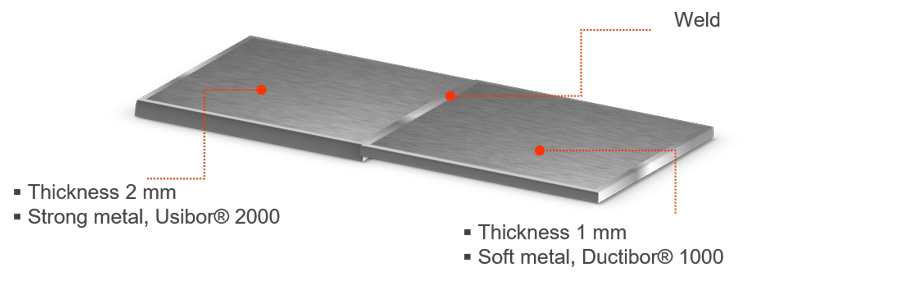
● Using laser welded blanks, automotive engineers can design parts with the necessary properties where they are needed, optimizing cost, weight and safety
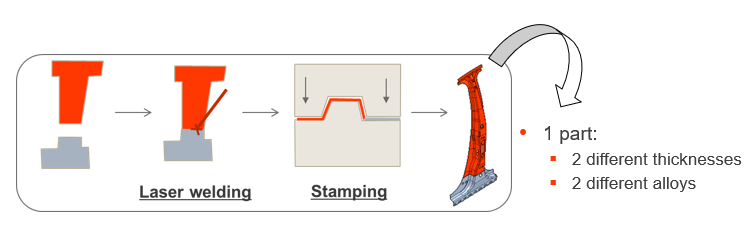
Optimisation of material use with LWB
● LWB allows to engage less raw material therefore reduce cost.
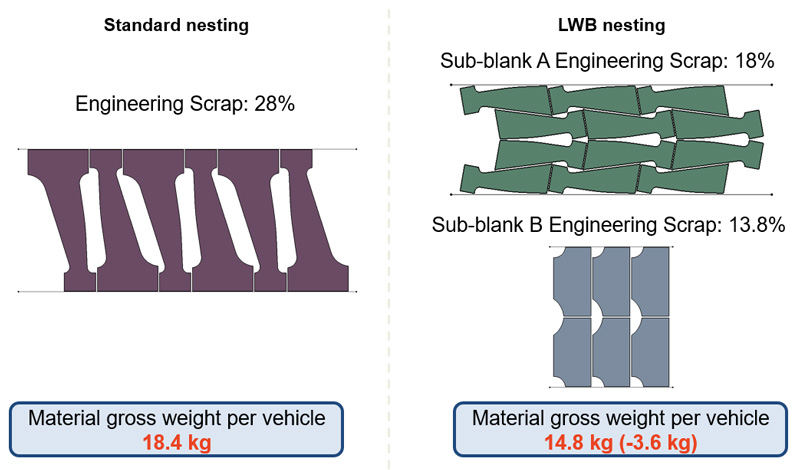
Laser Welded Blanks applications
● Optimum balance between light weight and strength thanks to LWB
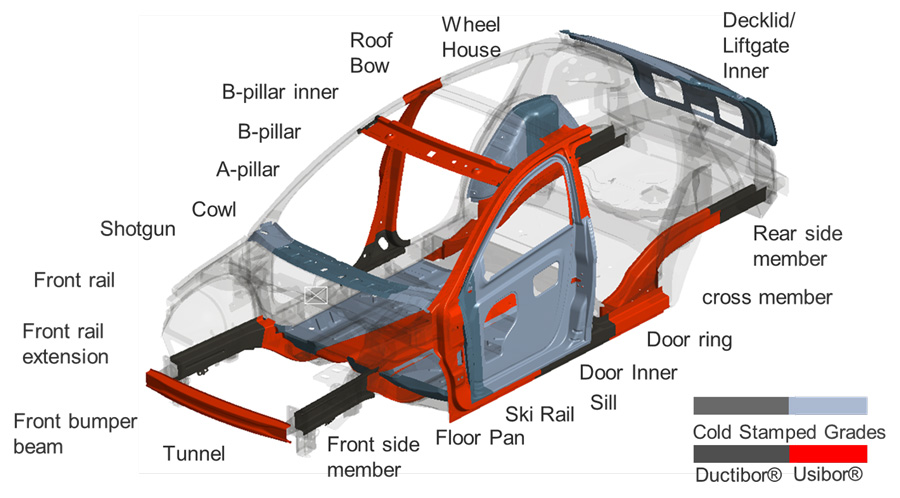
Laser welding of Press Hardened Steels
● Usibor® and Ductibor® are delivered with an Aluminum-Silicon (AlSi) coating
- The coating base composition is about 88 wt% Al + 12 wt% Si.
● The coating function is to:
- Avoid scale formation and surface decarburization during the thermal treatment process
- Protect the final part against corrosion.
● At delivery state, the AlSi coating is typically composed of 2 layers:
- A pure Al layer with local Si enrichment, thickness of 15 – 30 µm,
- A very hard intermetallic layer (Fe2Al5 + FeAl3) at the interface with the steel substrate, thickness of 5 - 10 µm.
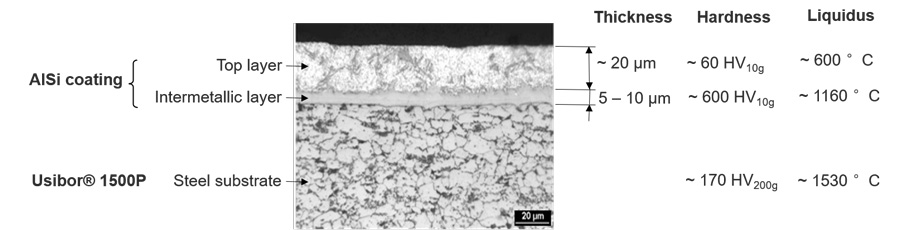
Weld pollution with conventional laser welding
● During butt laser welding, the aluminum coating is mixed with the molten steel and pollutes the weld
- At high Al concentration à formation of brittle intermetallic particles
- At low Al concentration: modification of the microstructure, leading to a soft weld (while the base metal is hardened by the hot stamping process)
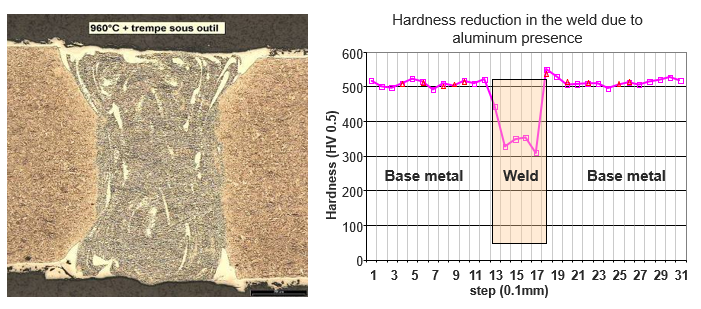
Coating removal is indispensable prior to laser welding
● Al pollution decreases significantly the weld properties. And failure occurs along the Al-rich areas
Failure of weld in a dynamic tensile test
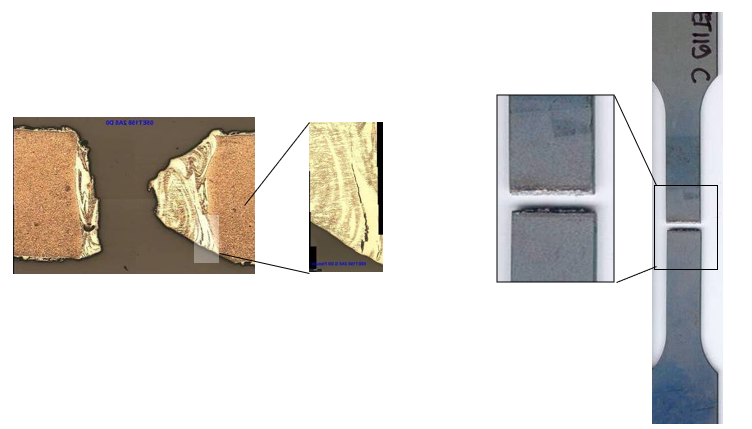
● Example: conventional butt welding of Usibor® 1500 blanks, iso-thickness 1.75mm/1.75mm,
- Ultimate tensile strength = 1139MPa
- Yield strength = 531MPa
Dedicated AlSi coating removal process
● Before laser welding, the AlSi coating near the edge is partially ablated by laser
- Top layer removed to avoid excessive Al dilution in the weld
- Thin intermetallic layer intentionally kept to guarantee corrosion protection
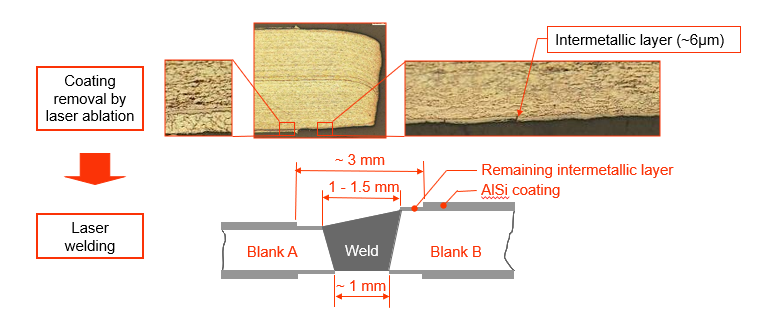
● ArcelorMittal process limits Al-content in weld, guaranteeing weld quality
Simplified process and robust product quality
● All GONVVAMA plant are equipped with state-of-the-art laser ablation lines
● After ablation, the part can be welded by standard laser welding line
● Main benefice for the weld
- Homogeneous microstructure after heating treatment and quenching
- Almost same hardness in the weld and in the base metal
- Fracture occurs in base metal