On May 24th, 2018, VAMA Gonvarri Advance Automotive Steel Solutions (Shenyang) Co., Ltd. (hereinafter referred to as GONVVAMA Shenyang ATS) officially held the SOP ceremony. In the first phase of the construction of GONVVAMA Shenyang ATS, 1 blanking line with capacity of 1,250 tons, 2 laser ablation lines and 2 laser welding lines were completed. The installation and commissioning of the ATS has been completed in May 2017 and started production then.
Opening Ceremony
![]() Shenyang ATS Plant Manager Mar Li presided over the ceremony
|
Speech by GONVVAMA CEO Mr. Jean-Marc Butin
|
Speech by Gonvarri CEO Mr. Josu Calvo
|
Speech by VAMA CEO Mr. Fernando Teixeira
|
Technical presentation by
VAMA CTO Mr. Li Xiang
New steel grades for lighter and safer car body structures
|
Technical presentation by
GONVVAMA CTO Mr. Yannick Yin
New carbody design enabled with advanced material & processing tech
|
Technical presentation by
ArcelorMittal Senior Engineer R&D Mr. Jean-Noel Gacel
New trends in EV body-in-white concepts
|
GONVVAMA is a joint-venture between VAMA and Gonvarri with 50% to 50% share partition. The headquarter of GONVVAMA is located in Changshu (Jiangsu province) and 4 Advanced Technologies and Solutions Centers are established in Shenyang, Changshu, Chongqing and Loudi, covering the major automotive clusters in China, helping carmakers meet the challenges of lightweight, safety improvement and environmental protection. The operation and SOP of GONVVAMA Shenyang ATS provide excellent processing services for customers as represented by Changshu/Shenyang, penetrate into the main automotive industry cluster in northeast China and bring the world's most advanced integrated technology solutions.
As the extended supporter of VAMA’s downstream industry chain, GONVVAMA focuses on the integrated forming of hot formed steel, advanced high-strength steel, ultrahigh-strength steel and exposed steel plates, and processing service of laser welded parts (LWB) with a view to providing quality products and integrated technical service solutions to automotive manufacturers.
Greener, lighter, and safer car body solutions with steel
The global automotive industry operates within a busy regulatory environment. This is certainly the case here in China, and the regulatory framework is quickly becoming stricter and more demanding. The challenge for carmakers is to meet the regulations within the very short timescales set by authorities.
The regulations have two main goals:
1. Drastically improve fuel efficiency in China’s car fleet, with a fuel-consumption target of 5 liters per 100 kilometers by 2020. A further target of 4.5 liters per 100 kilometers is anticipated after 2020.
2. Achieve Euro 6 emission levels by 2020.
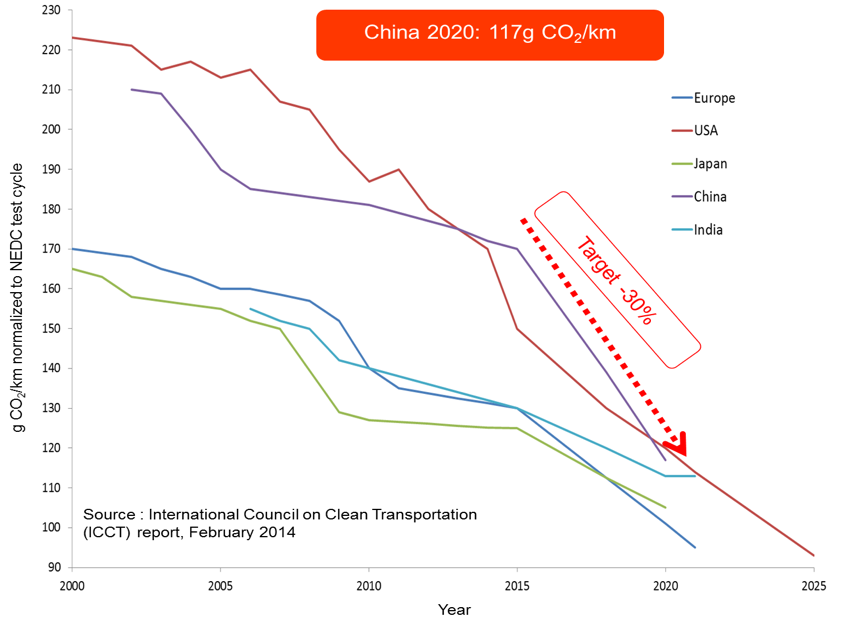
Safety is also the subject of new regulations. It is very likely that new crash management standards will be in place in China by 2018. Crash safety requirements are expected to match those of the US.
Another issue facing carmakers is supply chain reform. The government wants to see China’s industry move from a pure manufacturing base to one with higher technology content. The government also believes that there should be greater domestic ownership of the key and emerging technologies that are driving the industry.
The latter resonates with China’s domestic carmakers who are receiving strong signals from the government to upgrade the technology content of the products they are developing and selling.
China’s government wants to ensure that solutions and products are available locally. They want the automotive industry to strive for self-sufficiency in innovation, and the supply components, rather than relying on imports.
As a worldwide leader in steel production and solutions, ArcelorMittal has established a steady footprint in China with VAMA. The equal-share joint venture between ArcelorMittal and Valin Steels provides a full range of automotive steels, from mild grades to steels with very high strength. Hot-stamping grades such as Usibor® 2000 and Ductibor® 1000 are also produced by VAMA. These grades are already widely used in the Chinese market and allow carmakers to meet requirements on crash safety, weight saving, and emissions reduction.
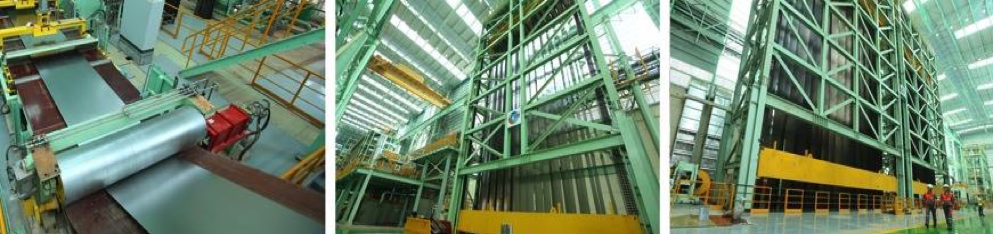
Global technology with local availability
ArcelorMittal’s aim is to supply more than just products, they also aim to be a solution provider. With the success of VAMA, ArcelorMittal decided to extend its supply chain and bring its downstream technologies to the Chinese market. A new joint venture, GONVVAMA, was created to offer the most advanced solutions to Chinese customers.
Known as VAMA Gonvarri Advanced Automotive Steel Solutions Co. Ltd (GONVVAMA), the venture is an equal-share partnership between VAMA and Gonvarri Steel Services. Gonvarri is a global leader in steel processing and distribution.
As a downstream solution provider for automotive steel, GONVVAMA will be integrated into the VAMA supply chain. It will act as one channel to VAMA’s clients.
Thanks to the technology transferred from ArcelorMittal, GONVVAMA will operate the latest manufacturing technologies to produce monolithic blanks and laser welded blanks (LWB) in steel. Both cold- and hot-stamping products will be used including Usibor® 2000 and Ductibor® 1000, third generation ultra-high strength press hardenable steels, and exposed panels.
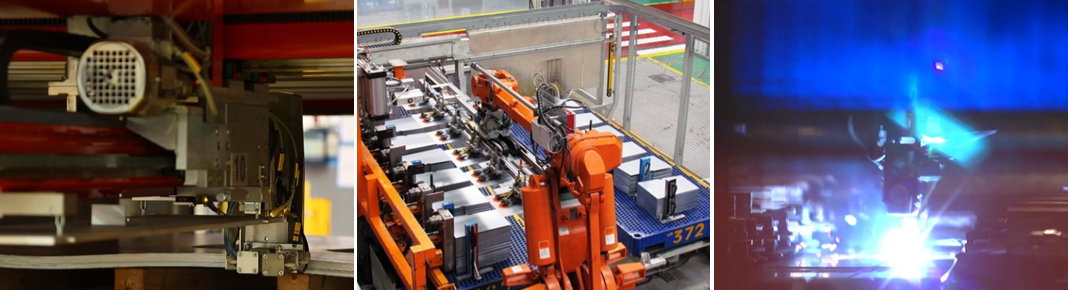
Headquartered in Changshu, GONVVAMA currently operates four advanced technology centers (ATS) in Loudi, Changshu, Shenyang, and Chongqing. The ATS cover all of the major automotive clusters in China.
As part of the joint venture, every GONVVAMA ATS will be equipped with best-in-class shape blanking and laser welding processing lines. The lines will employ ArcelorMittal’s proprietary technologies and make use of the company’s extensive experience with automotive steels. Through its own network of strategic steel service centers (SSC) and partners across China, GONVVAMA will offer customers a full range of steel services and solutions.
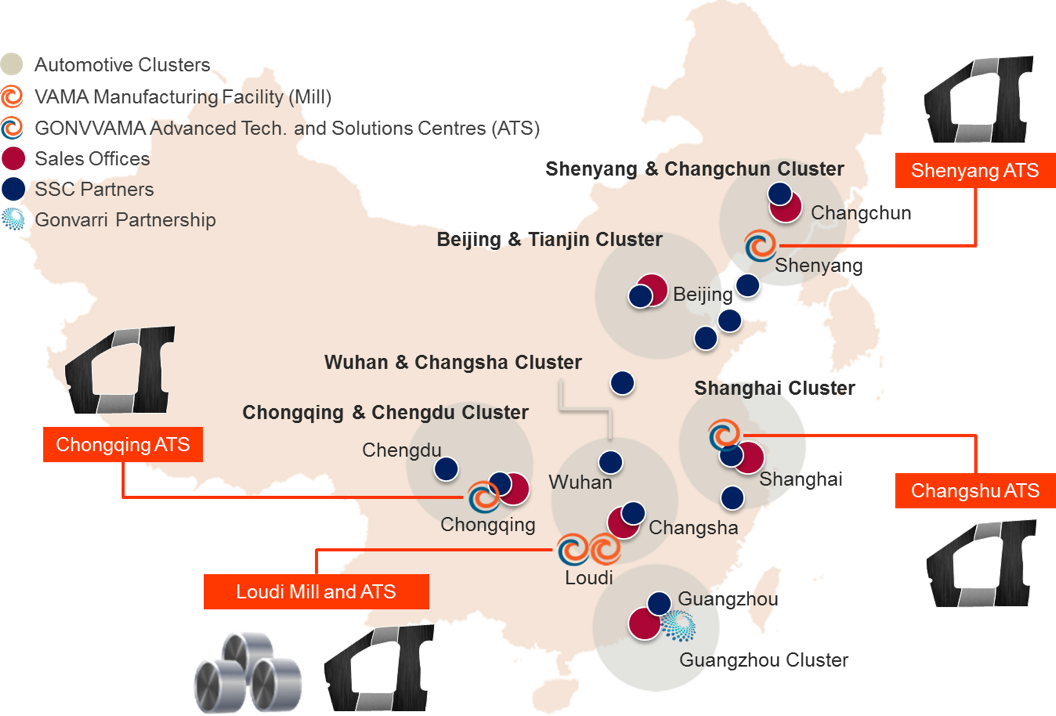
Innovative car body concept
Thanks to the technical support provided by ArcelorMittal, revolutionary new concepts will be available to GONVVAMA’s customers. These include hot stamped LWBs for the vehicle’s safety cage, a concept which is booming in EU and US markets. The proven solutions not only increase the safety of the passengers, they also play an important role in reducing the weight of the body-in-white and cutting assembly costs.
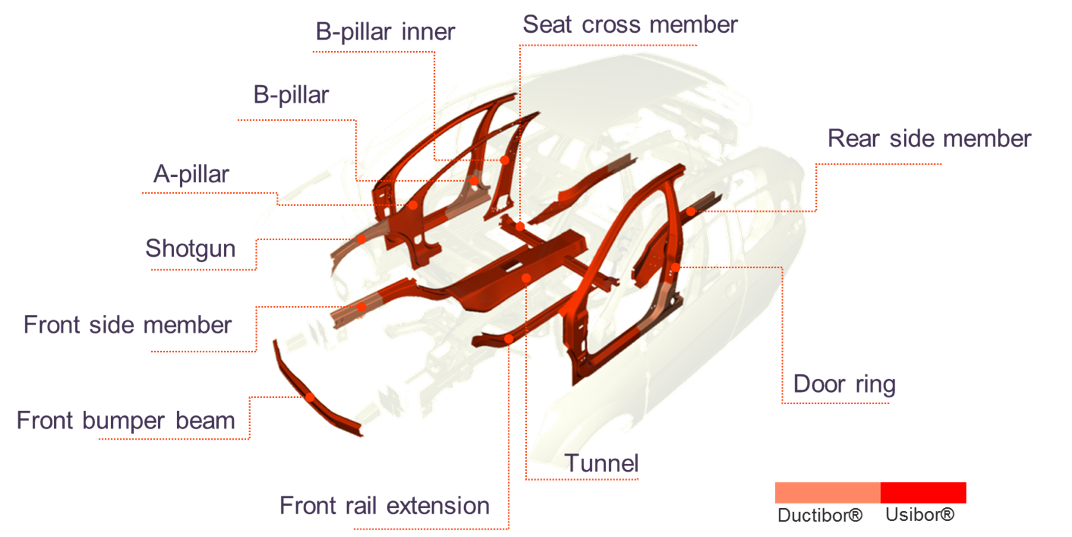
ArcelorMittal’s single-piece door ring is a perfect example of the benefits of LWB technology. Instead of ten parts, the door ring is formed from a single LWB. As well as reducing material costs via effective nesting and optimization, the manufacturing process is simplified. The performance of the part is enhanced thanks to continuous laser joints and new materials.
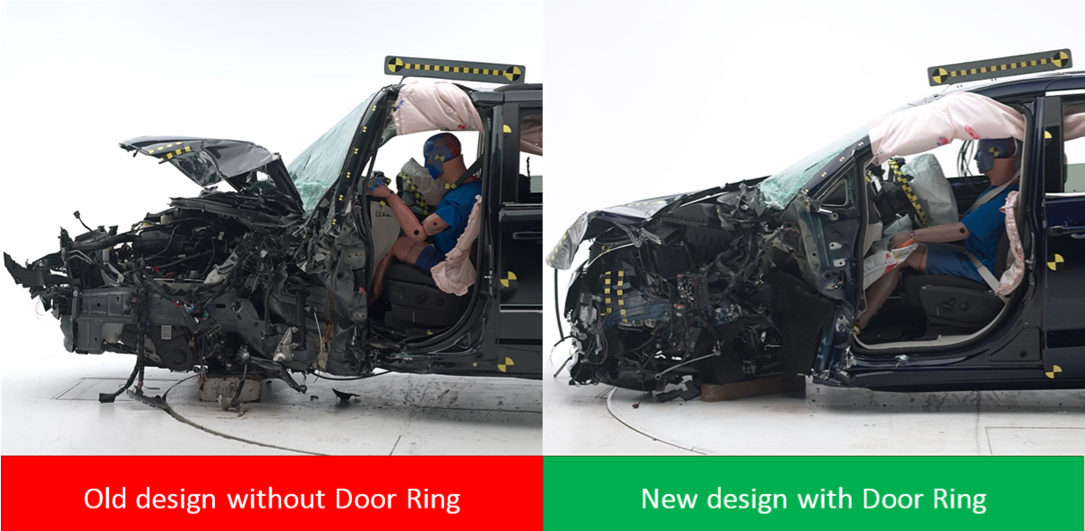
Over the past decade, ArcelorMittal has developed a number of generic steel solutions under the S-in motion® brand. Solutions include the body-in-white of C-segment vehicles, closures, chassis parts, and seats for cars. S-in motion® solutions offer a catalog of the lightest vehicle designs and use currently available AHSS grades. They integrate worldwide crash, stiffness, and performance standards at the lowest possible cost. For example, the ArcelorMittal S-in motion® mid-size SUV solution allows carmakers to achieve weight savings of 112 kg on the body-in-white and closures (compared to the baseline). The solutions can be implemented without jeopardizing safety and at nearly the same cost.
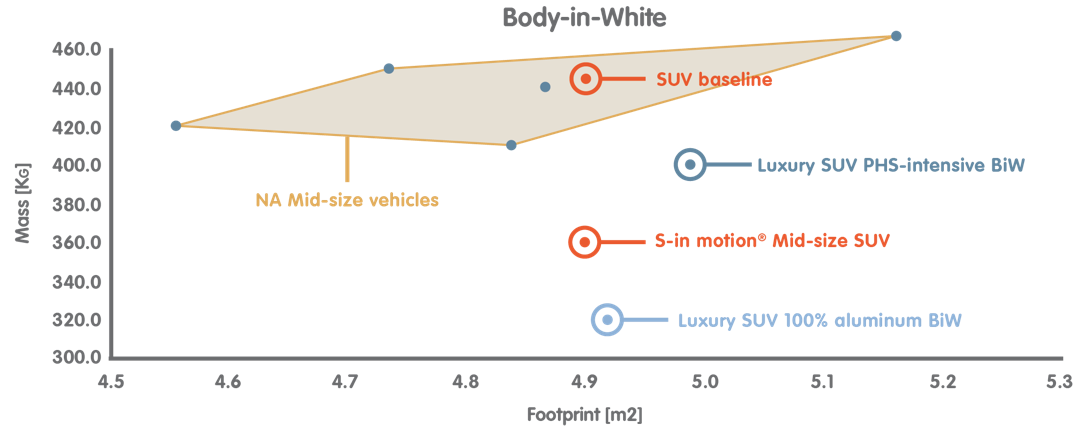
With the integration of ArcelorMittal technology into GONVVAMA plants, those solutions are available on the doorstep of Chinese customers today.
Electrical vehicles (EV) – the new trend
The role of AHSS in EV production is becoming increasingly important, particularly for China. By 2020 China aims to produce two million electric cars, with that number doubling by 2025. Weight savings in this type of vehicle are crucial as the battery itself accounts for much of the car’s overall mass.
The integration of a heavy battery and removal of the internal combustion engine leads to drastic changes in the mass and balance of the car and creates new crash management challenges. The battery and its cover also require significant safety and crash protection. There is a strong push to use AHSS in this type of car to achieve the required safety and weight reductions.
ArcelorMittal Global R&D and GONVVAMA have been developing specific S-in motion® solutions for electric vehicles which will meet Chinese regulations. The award-winning solutions, integrating the most advanced AHSS and hot stamping grades, help carmakers to achieve excellent crash safety performance with considerable weight savings, and almost no increase in cost.
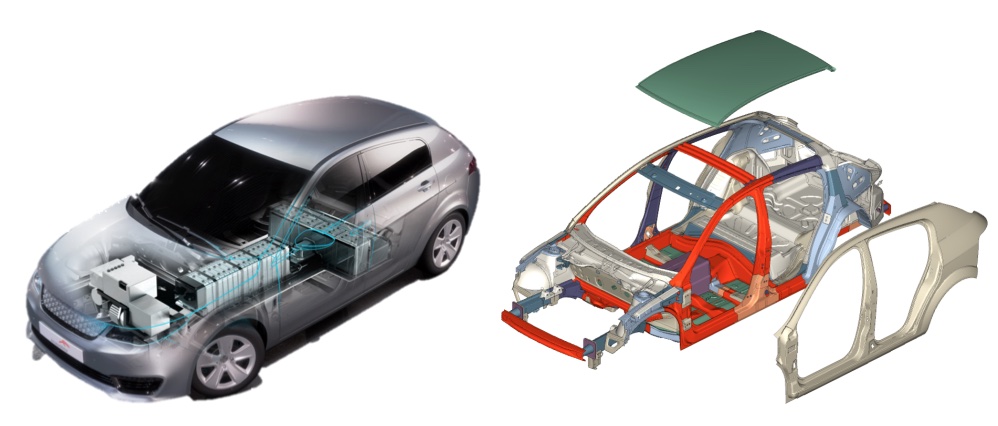
Through knowledge transfer from Gonvarri, GONVVAMA will consolidate its leading technical position in the blanking of exposed steel parts. This will complement GONVVAMA’s existing steel solution catalogue.
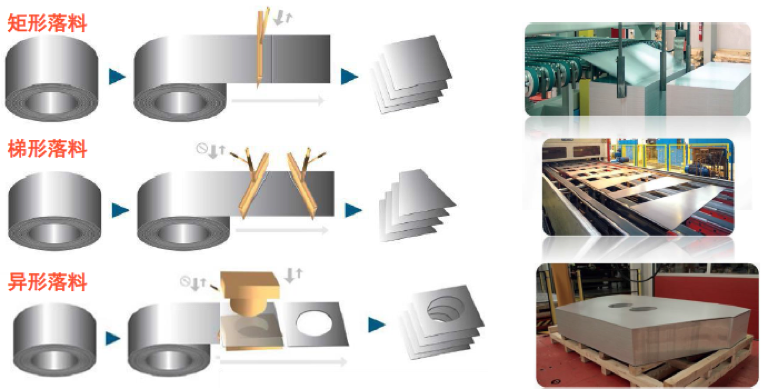
Early vendor involvement
ArcelorMittal also brings competence in co-engineering. As regulations become more stringent, OEM design centers in China are working quickly to make the next generation of cars safer and lighter. Thanks to R&D support from ArcelorMittal, GONVVAMA works directly with these design centers. We can provide them with our expertise on tailor-made solutions and applications for the body-in-white. Nesting and formability studies of LWB parts and the integrated supply chain will be carried out to help customers improve production efficiency and product performance.
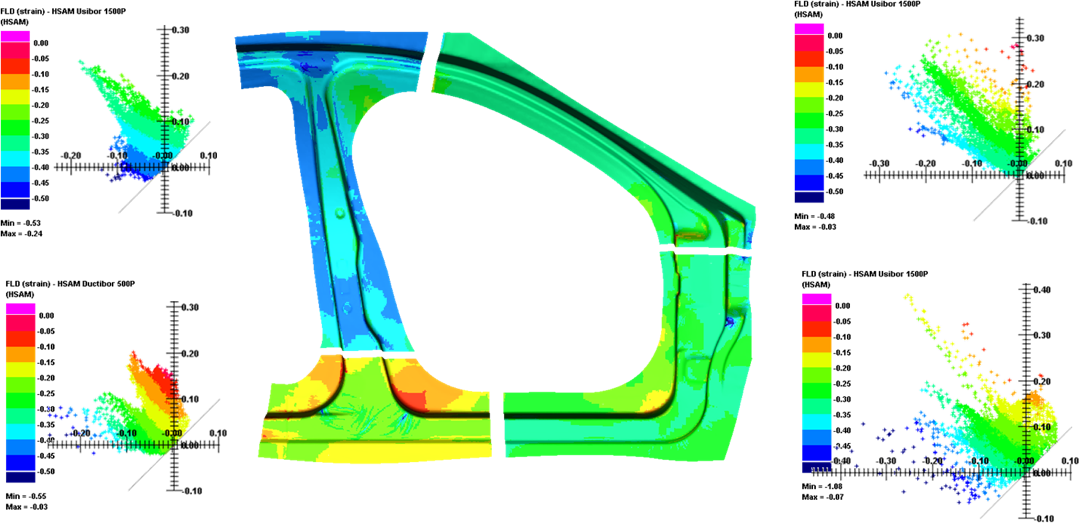