Recently, AI Automobile Industrie Magazine, a subsidiary of Vogel Industries Germany, released the list of top 10 innovation technologies of auto parts in 2016. Arcelormittal’s new generation of high strength steel Usibor® 2000 and Dcutibor® 1000 entered the list because of it’s strength, and great potential in lightweight car body.
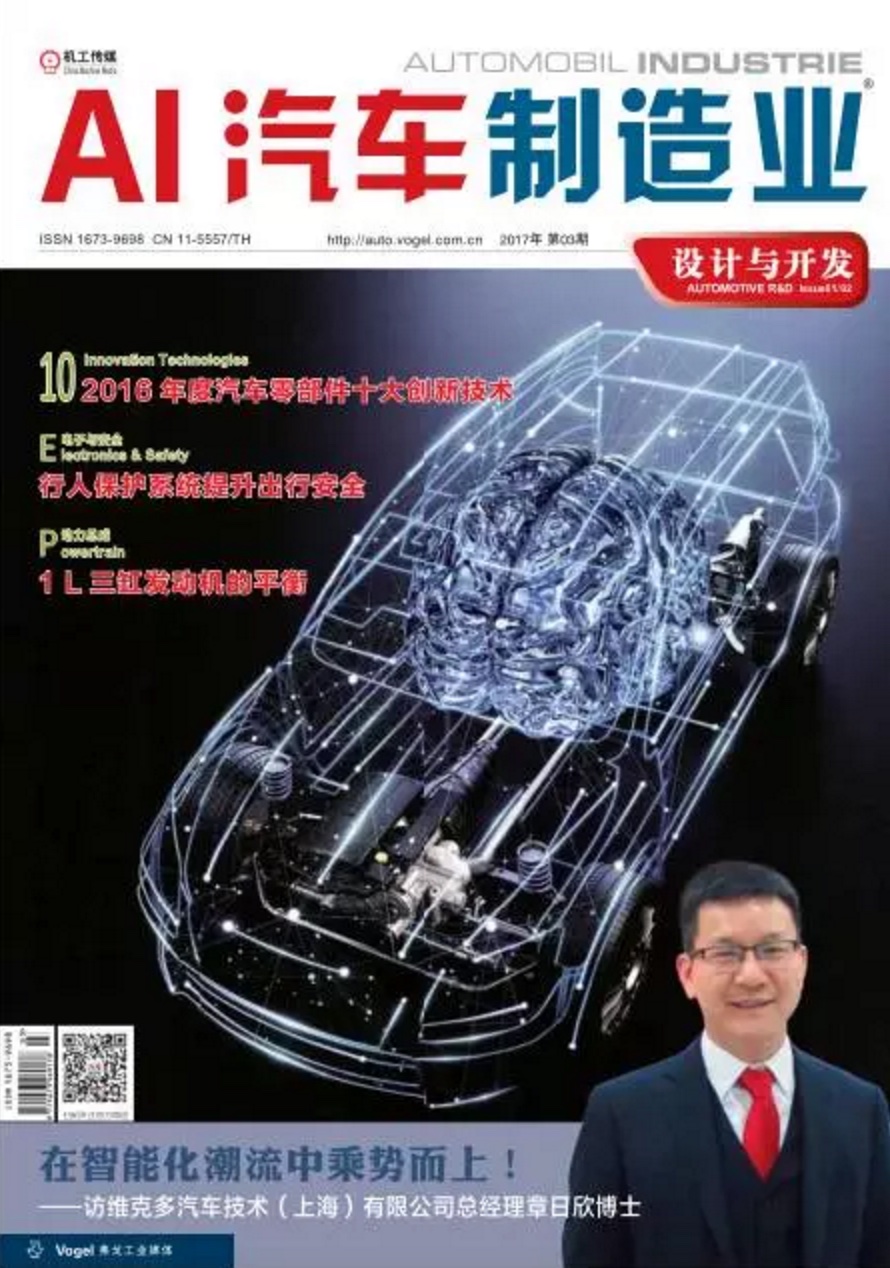
Following Usibor®1500 and Ductibor®500, Arcelormittal released the second generation of high strength steel products Usibor®2000 and Ductibor®1000. Compared with the first-generation, the new products increased by 30% in strength, reaching up to 2000 Mpa; At the same time, it has the characteristics of excellent corrosion resistance and complex parts do not rebound after stamping, these characteristics can help the automobile manufacturers achieve the goal of mass reduction within the reasonable cost. Currently Usibor®2000 and Ductibor®1000 are certified by OEMs on European market will be certified on North American market at the beginning of 2017.
With laser welding technology, Usibor®2000 and Ductibor®1000 can be welded together, forming an integrated part. This technology allows OEMs to further optimize the design of the vehicle, apply different types of steel for the appropriate component parts, while effectively improve vehicle safety performance significantly, reduce weight, and lower the material cost, optimize the manufacturing processes to reduce the comprehensive cost.
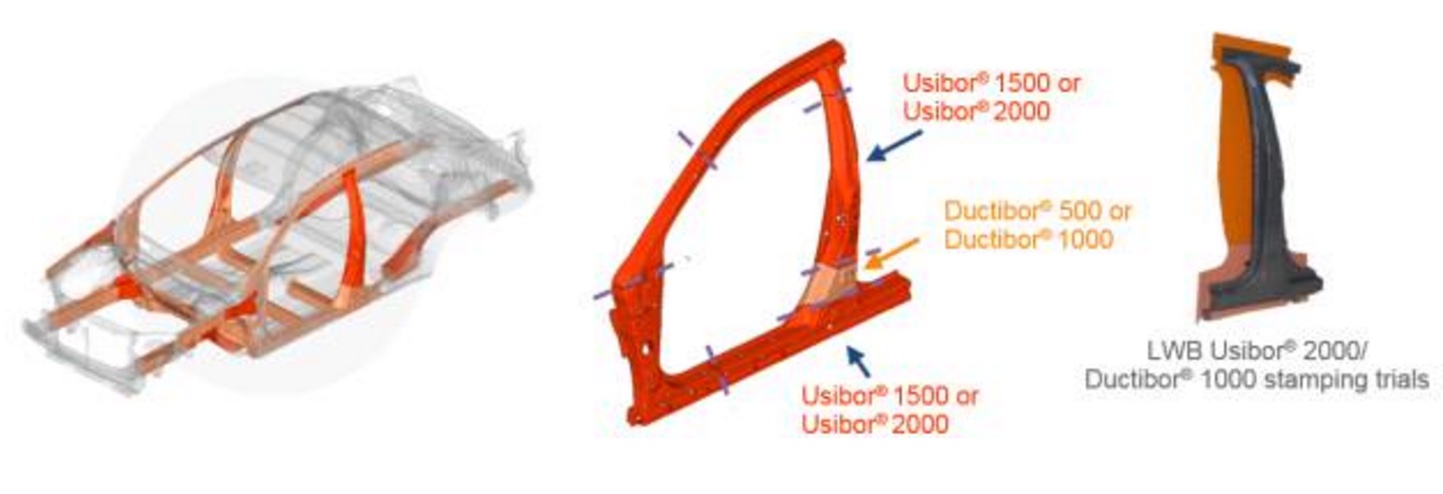
The new generation of Usibor® and Ductibor® can help OEMs to achieve the following goals:
- extremely high strength
- optimization of strength and ductility with laser welding technology
- no rebound after stamping of complex parts
- excellence in erosion resistance
Arcelormittal is now cooperating with several automobile manufacturers, will apply Usibor® and Ductibor® to the actual car models, and achieve outstanding achievments in body weight reduction and impact performance.
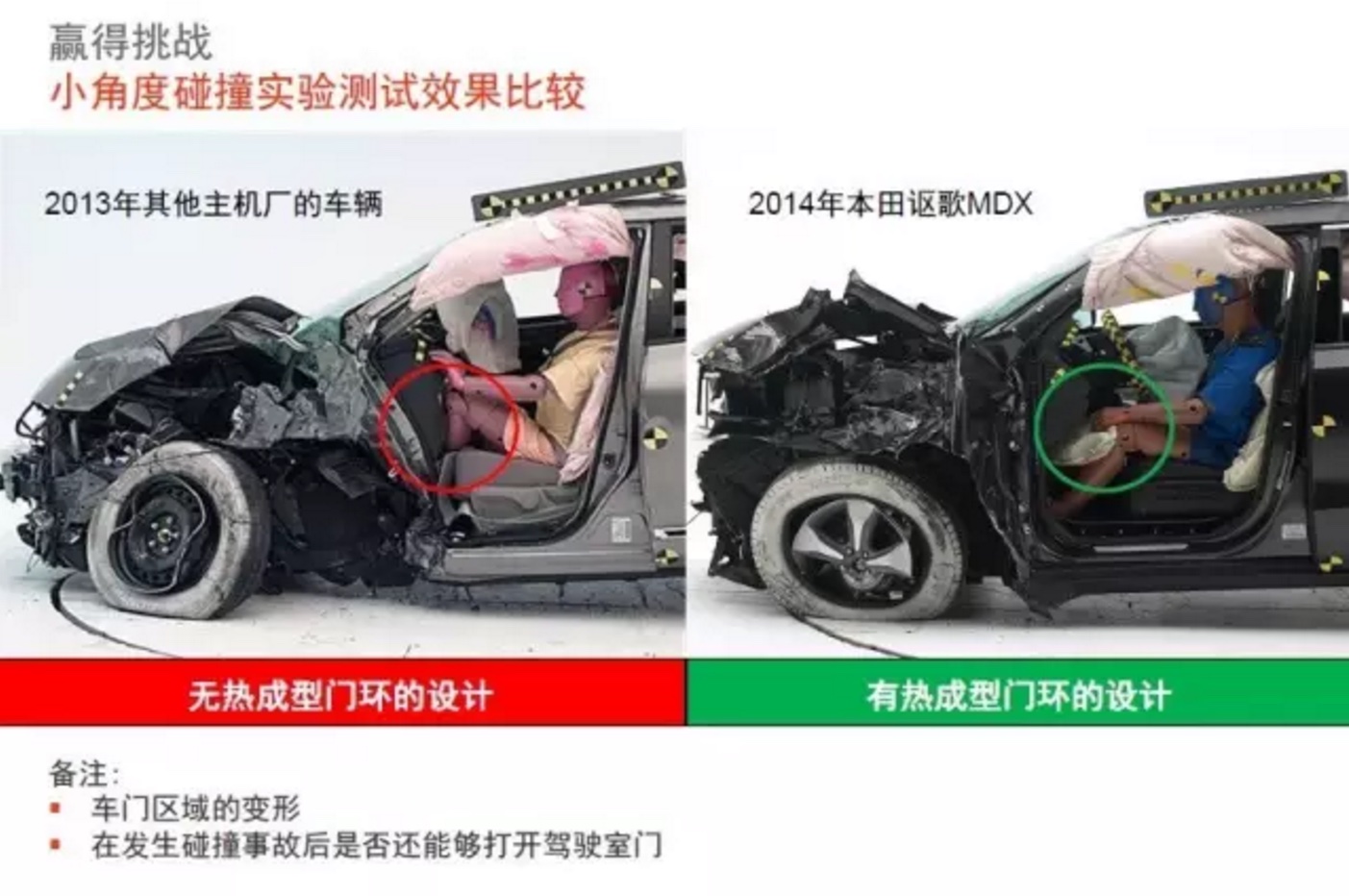
In 2014, the laser welded door ring first applied on Honda Acura MDX model technology
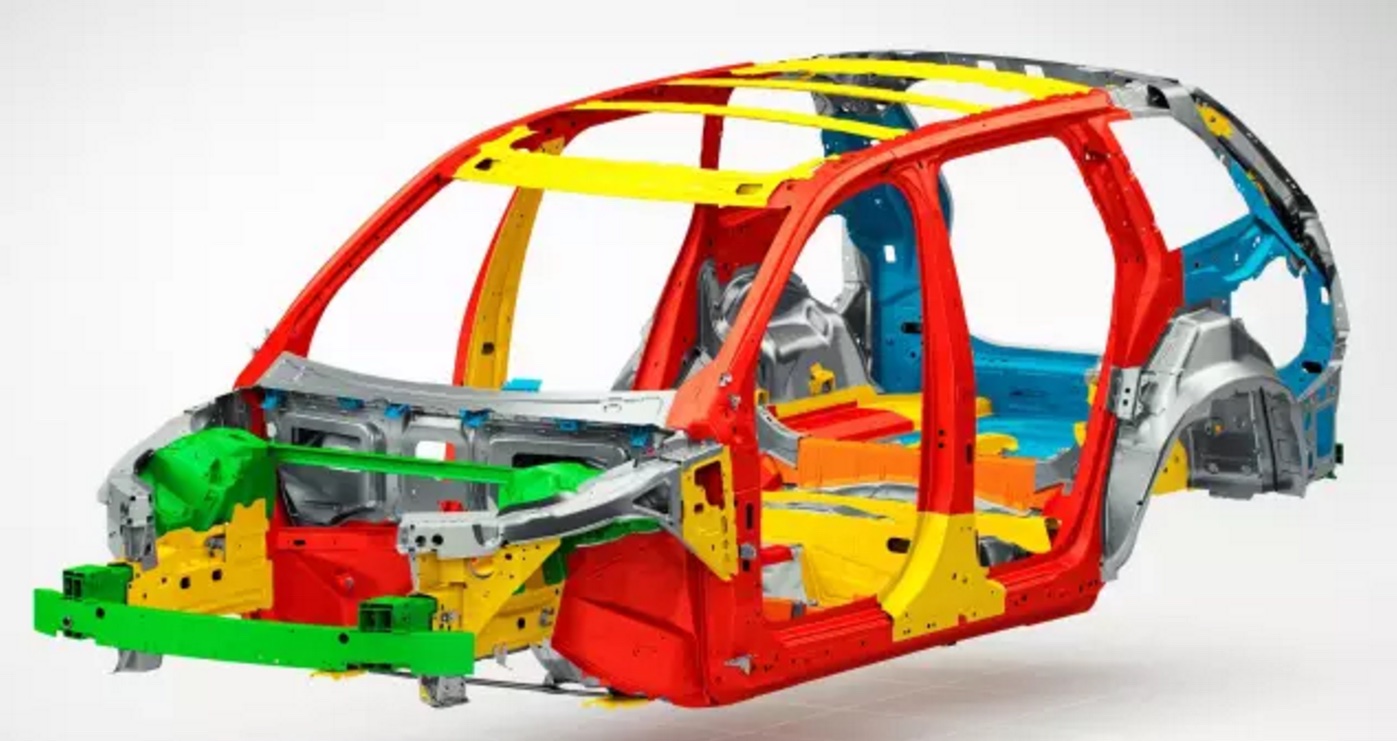
In 2015, Volvo launched the new XC90 SUV model, more than 40% of the body parts are made of hot formed materials, the model wins the the highest level of safety performance in Europe and North America IIHS NCAP assessment
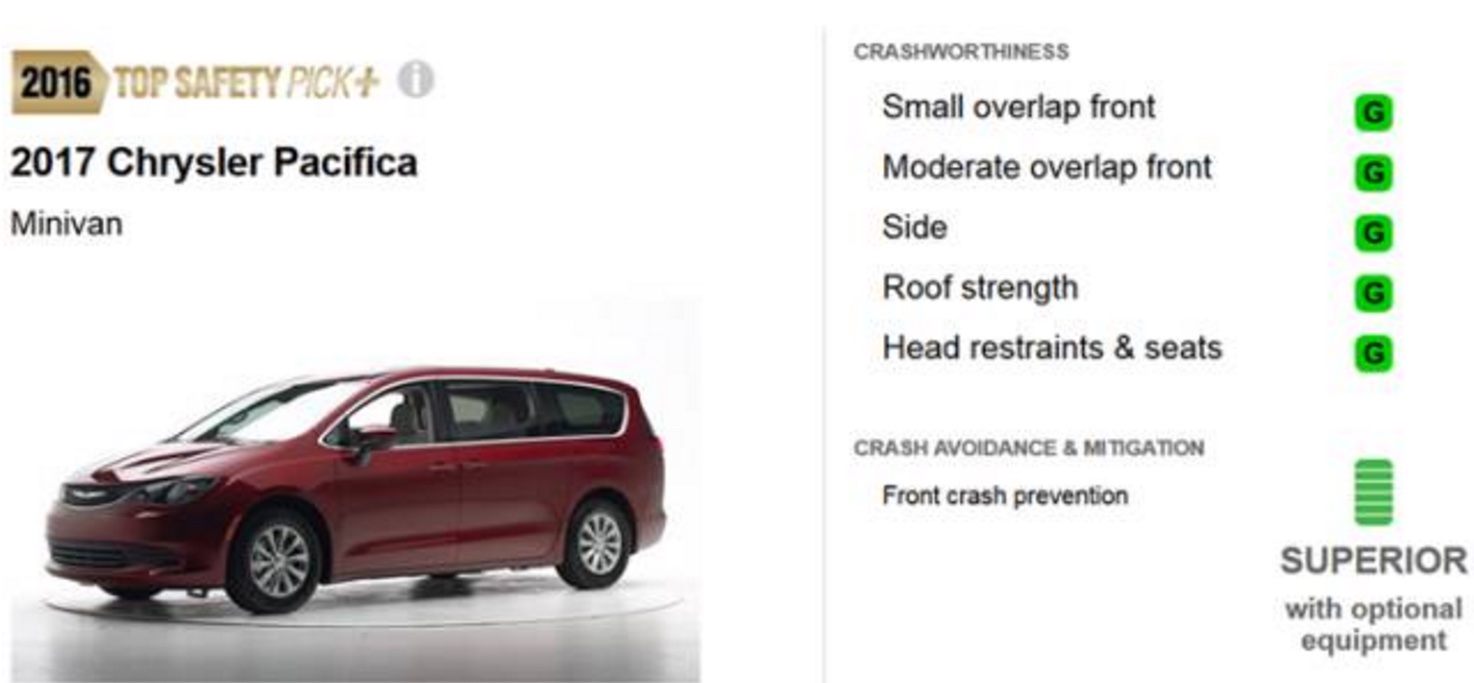
In 2016, Chrysler Pacifica model with Arcelormittal’s hot formed integrated door ring, integrated five parts into one, effective achieved a weight loss of 8.64 kg, and significantly improve vehicle safety performance
As with Al-Si coated high strength stee, Usibor®2000 can increase by over 30% in strength compared with the previous Usibor®1500. Compared with the current hot forming solution, Usibor®2000 can achieve a reduction of 10% to 15% in weight. Compared with Usibor®, Ductibor® has higher ductility, using laser welding technology, Usibor®2000 and Ductibor®1000 can be made into integrated parts, making the performance of the two materials effectively complement to each other, thus ensuring the correct material is applied to the right place. This technology can improve the safety and impact performance of auto parts and reduce the car body weight.
AI Automobile Industrie Magazine highly appraised Usibor®2000 and Ductibor® products:
Arcelormittal's 2nd generation of hot formed high strength steel Usibor®2000 and Ductibor®1000 products have largely improved in various performance aspects, especially the tensile strength of 2000 Mpa. They’re industry-leading products and can help the automobile manufacturers to better achieve the goal of lightweight.