安赛乐米塔尔公布世界上第一个内外门环系统,该解决方案是安赛乐米塔尔跟本田美国研发中心联合开发的成果,将应用在2019年讴歌RDX车型上。
2018年4月19日—芝加哥—安赛乐米塔尔多年来一直同汽车制造企业合作进行钢材解决方案的联合开发,从而以最经济的方式来应对安全、强度和燃油经济性的要求。安赛乐米塔尔提供了一希列轻量化钢材解决方案,在同本田美国研发中心共同开发门环解决方案的工作上取得了巨大进步。
“安赛乐米塔尔和本田合作的历史可以追溯到十年前。我们很荣幸能够安排我们的工程师在本田驻厂,寻找优化钢板以及材料应用的有效方式,并且更好地了解客户需求。” — 安赛乐米塔尔激光拼焊板美国公司(AMTB)总裁 Todd Baker说道。
通过合作,安赛乐米塔尔和本田在2014年的讴歌MDX上带来了业界第一个热成型激光拼焊外门环。外门环-车身结构的关键零件,能够给予汽车强度和刚度—取代了传统的多块、点焊的设计。该项技术也应用在本田的其他车型上,包括Pilot和奥德赛。
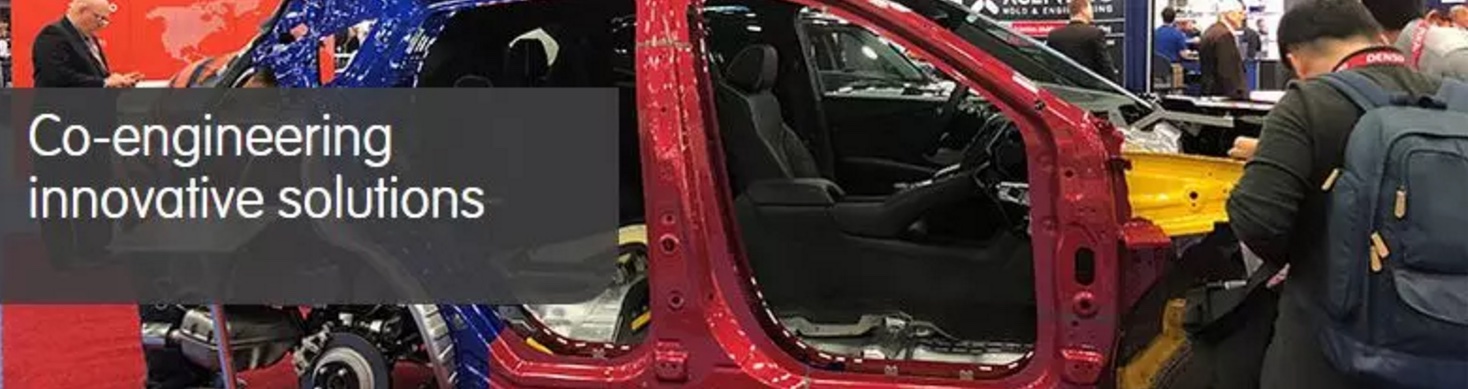
2018年4月10日-12日,在美国COBO Center会展中心举行的2018年美国底特律国际汽车设计工程展览会上,合作双方公布了世界上第一个内外门环系统,在进一步减轻车身重量的同时,更好地平衡强度和性能。
“汽车的前部车身结构—或者是驾驶员和乘客周边的区域—由一个环构成,这个门环是安全笼式车体的关键部分。外门环是连接车门和汽车外饰的部位,而内门环是安全气囊和所有汽车内饰所依附的部位。两者结合在一起,组成了一个连续的前车门结构,提供了一个非常稳固的解决方案”。 — 本田美国研发中心的讴歌RDX车身开发负责人Joe Riggsby说道。
内门环由五块不同厚度规格的Usibor® 1500(安赛乐米塔尔专利压力硬化钢)组成,而内门环是由四块不同厚度规格的Usibor® 1500组成。各种Usibor®钢材先在落料公司进行落料,接着发往AMTB在底特律的新工厂。落料后的钢板在这里通过激光去镀层工艺来保证最终成品的性能。去镀层后,钢板被拼焊接在一起,再经过多道质量控制程序来保证精度。接着拼焊板会被发往热冲压厂,在那里冲压成汽车客户所需要的成品零件。
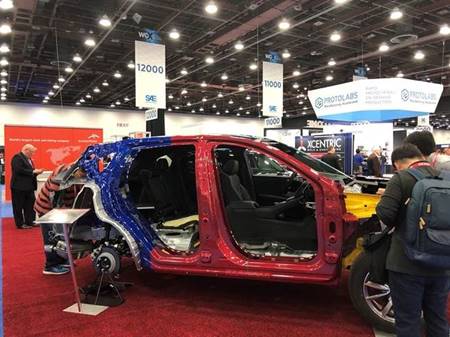
“内外门环系统将我们的安全保护带入更高的级别。该解决方案能够管理汽车前部的碰撞载荷,并将其传递至通过车身后部结构。它同时能够平衡侧面碰撞以防止驾驶室侵入,从各个方位保护乘客。这个汽车还装配有全景天窗,再加上两个门环,性能真的非常棒。” — 本田美国研发中心的讴歌RDX车身开发负责人Joe Riggsby说道。
除了能够提高汽车性能和安全,包括在小偏置碰撞测试中取得5星的成绩,门环解决方案还能够帮助汽车制造企业实现其轻量化目标。本田在RDX车型上使用了50%以上的超高强钢,跟上一代车型相比,车身重量降低了19kg/42lbs。
“我们看到门环和我们的热成型解决方案继续在业内推进。我们正在同更多的客户合作将他们应用到更多的车型上去,我们看到这个解决方案正在更多地应用在更多的汽车型号上。该方案的应用不仅仅局限于SUV和MPV,我们同时也看到它在皮卡车和小型乘用车上使用。这也验证了我们的信念,也就是门环和热成型激光拼焊板是一种性价比很高的,能够使汽车更安全更轻量化的技术。” — 安赛乐米塔尔激光拼焊板美国公司(AMTB)总裁 Todd Baker说道。
如需了解更多,请点击查看这个视频“安全规则改变者”